Major Inventory Problems and Solutions
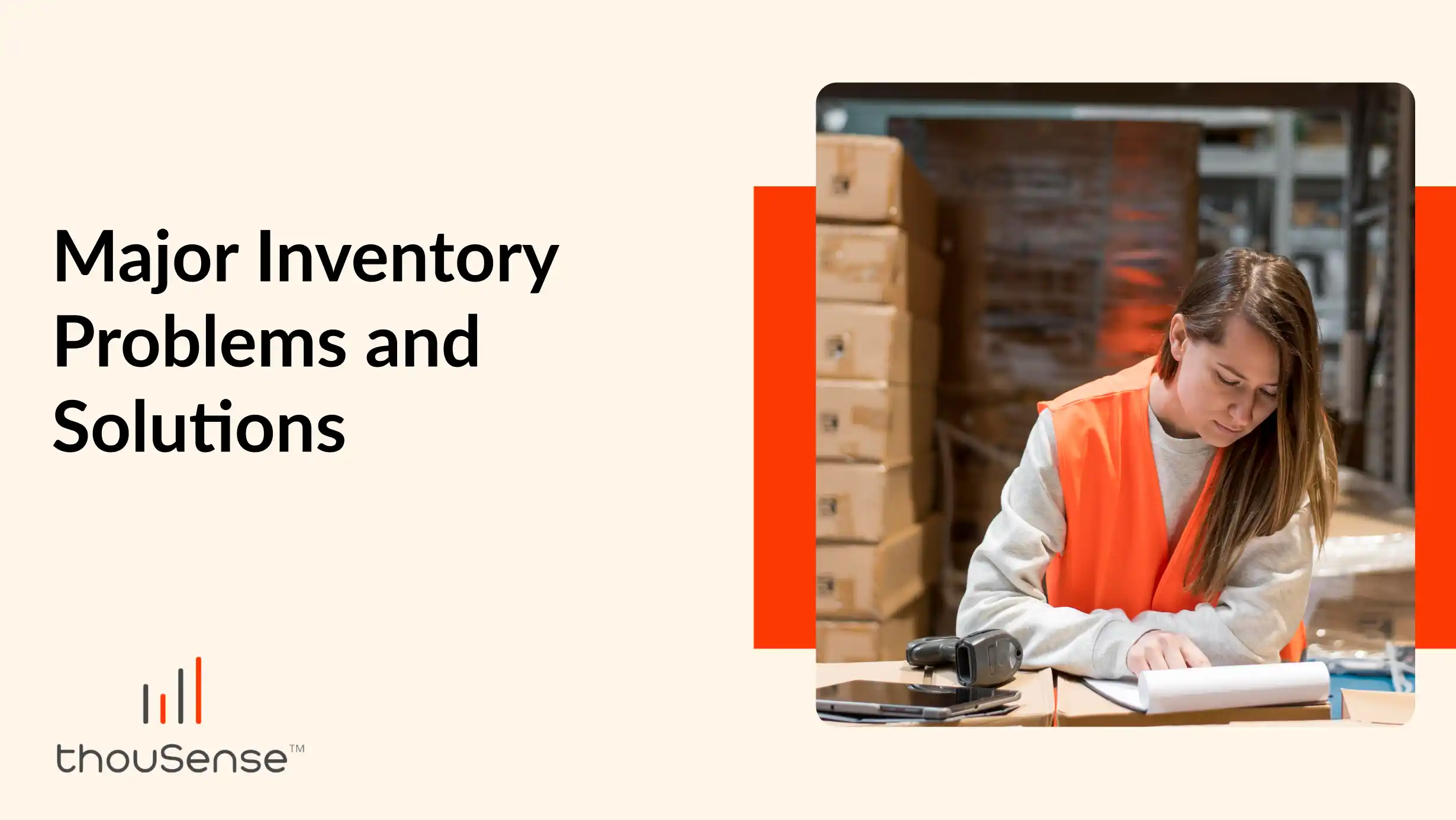
Inventory management is the cornerstone of a thriving business. Whether you're running a large retail chain or a small e-commerce store, keeping track of inventory is critical to meeting customer demands without tying up excessive capital. Unfortunately, poor inventory management can lead to severe financial losses, unsatisfied customers, and inefficiencies.
So how do you strike the right balance? The answer lies in understanding common inventory problems and their solutions, often supported by advanced tools like AI-powered demand forecasting. This blog dives deep into these challenges and their fixes, providing a roadmap to effective inventory management.
Why Inventory Management Matters?
Imagine going to a shop and not finding what you want because it’s sold out. Annoying, isn’t it? This is where keeping track of stock, called inventory management, comes in. It helps make sure customers always find what they need.
Good inventory management isn’t just about counting items. It touches every part of a business. It keeps customers happy and helps the business make money. Using smart tools like software that predicts what people will buy can make managing stock easier, faster, and better.
Let’s look at some big problems businesses have with inventory and how they can fix them.
8 Major Inventory Problems and Their Solutions
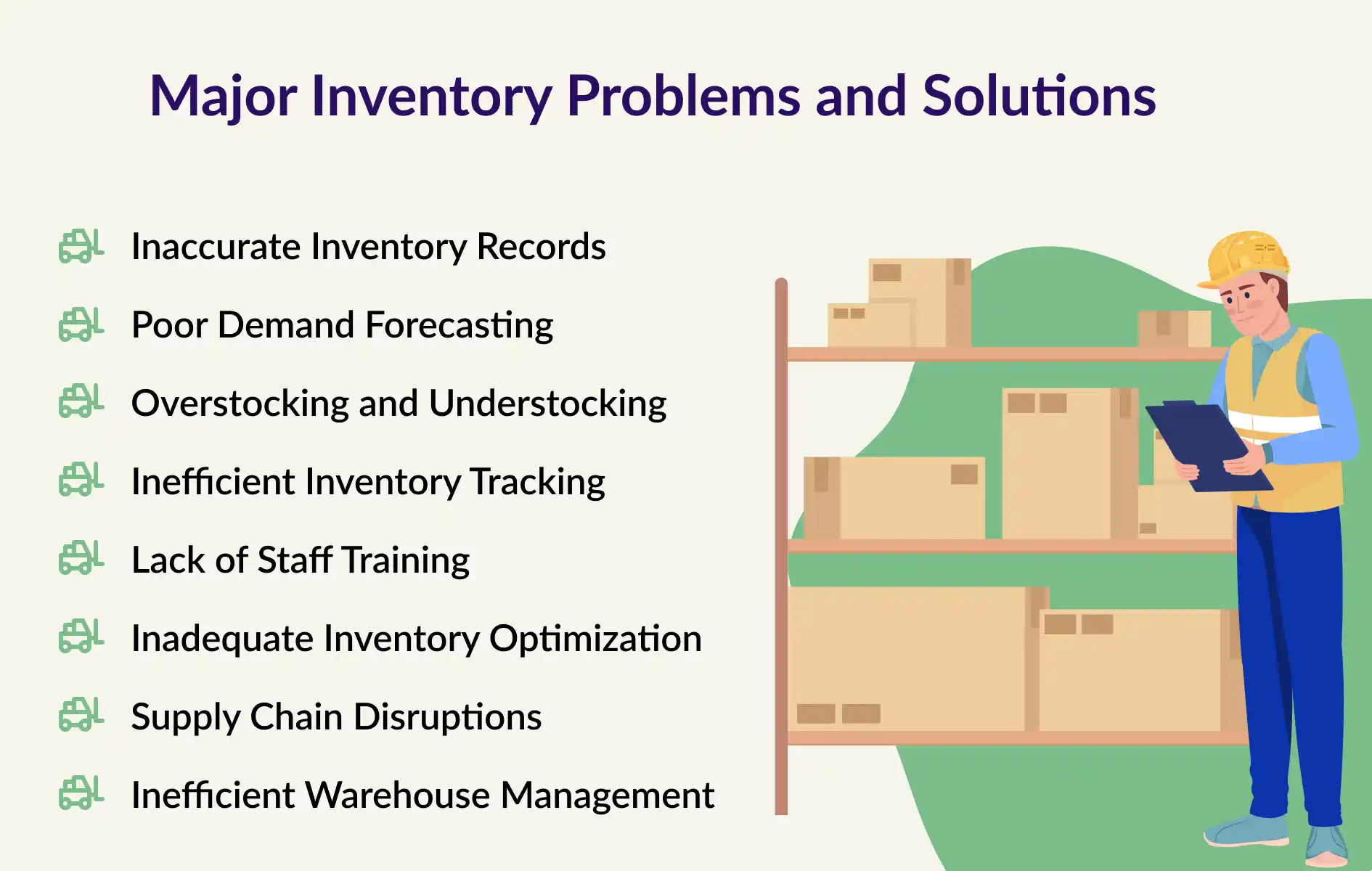
1. Inaccurate Inventory Records
Problem: The Invisible Gap
Ever wondered why businesses sometimes run out of stock despite having “enough” inventory on paper? Inaccurate inventory records are often to blame. A small error in tracking stock movements can lead to discrepancies, resulting in surprise stockouts or unnecessary overstocking.
Solution: Robust Inventory Management Systems
The fix lies in implementing inventory management software. These tools provide real-time visibility into stock levels, track inventory movements with features like barcode scanning, and generate detailed reports. Real-time updates ensure that discrepancies are caught and corrected immediately. Automation also reduces human error, making operations more reliable and efficient.
2. Poor Demand Forecasting
Problem: The Guessing Game
Poor demand forecasting is a silent killer in inventory management. When businesses fail to predict demand accurately, they either overstock (tying up capital and increasing storage costs) or understock (missing sales opportunities).
Solution: AI-Powered Demand Forecasting
Enter AI-powered demand forecasting software—the ultimate game-changer. By analyzing historical sales data, seasonal trends, and real-time market conditions, these tools predict demand with uncanny accuracy. Businesses can then plan their inventory levels more effectively, ensuring they have just the right amount of stock at the right time.
Schedule Your Demo Here:- https://thousense.ai/schedule-demo
3. Overstocking and Understocking
Problem: The Tightrope of Balance
Striking the perfect balance between overstocking and understocking is no easy feat. Overstocking inflates storage costs and risks product obsolescence, while understocking frustrates customers and leads to lost sales.
Solution: Just-in-Time Inventory Practices
Adopting just-in-time (JIT) inventory practices can be a lifesaver. This strategy minimizes excess stock by aligning inventory purchases with actual demand. Setting optimal reorder points using accurate demand forecasts ensures that you replenish inventory only when necessary, reducing waste and freeing up capital.
4. Inefficient Inventory Tracking
Problem: The Manual Chaos
Manual inventory tracking methods are outdated and error-prone. Relying on spreadsheets or paper records can lead to inaccurate counts, delays, and inefficiencies that ripple across the supply chain.
Solution: Automation to the Rescue
Automated inventory tracking systems eliminate these inefficiencies. With technologies like RFID tags and IoT sensors, businesses can monitor stock levels in real-time. These systems integrate seamlessly with other processes, such as order management, to ensure smooth operations from start to finish.
5. Lack of Staff Training
Problem: Untrained Hands, Unseen Losses
Even the best systems fail when employees don’t know how to use them. Untrained staff may mishandle inventory, enter incorrect data, or misinterpret reports, causing inefficiencies and errors.
Solution: Comprehensive Training Programs
Invest in staff training! Employees need to be well-versed in inventory management practices and software tools. Conduct regular workshops and provide access to updated training materials to ensure everyone is on the same page. A well-trained team is an efficient team.
6. Inadequate Inventory Optimization
Problem: The Hidden Costs
Failing to optimize inventory can inflate carrying costs and lead to stockouts during peak demand. Without clear priorities, businesses may overstock low-priority items and neglect high-demand products.
Solution: Data-Driven Inventory Optimization
Techniques like ABC analysis help categorize inventory based on importance and consumption patterns. Safety stock calculations further ensure that you have enough buffer inventory to cover unexpected demand surges. Optimization not only saves money but also boosts customer satisfaction.
7. Supply Chain Disruptions
Problem: The Ripple Effect
The global supply chain works like a big, connected web. If one part gets disturbed, it can mess up everything. You might end up with too little or too much stock. Things like natural disasters or political problems can cause major trouble for your inventory.
Solution: Building Resilience
To handle these problems, you need a strong supply chain plan. Work with many suppliers so you don’t depend on just one. Keep some extra stock for emergencies. Always have a backup plan. A Plan B can save you when unexpected events happen.
8. Inefficient Warehouse Management
Problem: The Warehouse Maze
A messy warehouse feels like a confusing maze. Things get lost, and it takes forever to find anything. This slows down your orders and wastes time and money. Poor layouts and bad tracking systems cause delays and mistakes.
Solution: Smarter Warehouse Practices
A well-organized warehouse works much better. Start by keeping things neat and tidy. Use technology to make packing and picking faster and easier. Label bins, check your inventory regularly, and use good software to manage everything. Even small changes like these can make a huge difference in how smoothly things run.
The Role of thouSense in Inventory Management
You might be thinking, “How does a tool solve all these problems?” That’s where thouSense steps in. With its smart, AI-powered features, thouSense is like a helper that makes inventory management easy and simple for businesses.

Key Features of thouSense
1. AI-Powered Demand Forecasting
thouSense looks at old data and live trends to predict what customers will need. This means businesses can plan better and avoid running out of stock.
2. Real-Time Tracking
The tool allows businesses to see their inventory clearly, in real-time. This means fewer mistakes and smarter decisions.
3. Optimization Tools
It also helps with smart tools like ABC analysis and automatic reordering. These tools make sure businesses have just the right amount of stock.
Conclusion
Effective inventory management is an ongoing process that requires a mix of strategy, technology, and human effort. From tackling inaccurate records to optimizing stock levels, businesses must address these challenges head-on to stay competitive.
Advanced tools like AI-powered demand forecasting software make this journey significantly easier, offering precise insights and seamless integration into existing systems. By properly using these tools, businesses can overcome inventory challenges, delight customers, and achieve long-term success.
So, are you ready to transform your inventory management? Start by embracing technology and adopting best practices. Your business—and your customers—will thank you for it.
FAQ's
1. What are the most common inventory management problems businesses face?
Overstocking, understocking, inaccurate tracking, poor demand forecasting, and inefficient processes lead to high costs, lost sales, and operational inefficiencies are some of the most common inventory problem which businesses face.
2. What are effective solutions to inventory management problems?
Use inventory software, adopt JIT practices, leverage demand forecasting tools, categorize inventory, and conduct regular audits to streamline operations and improve accuracy are some of the effective solutions for inventory problems.